
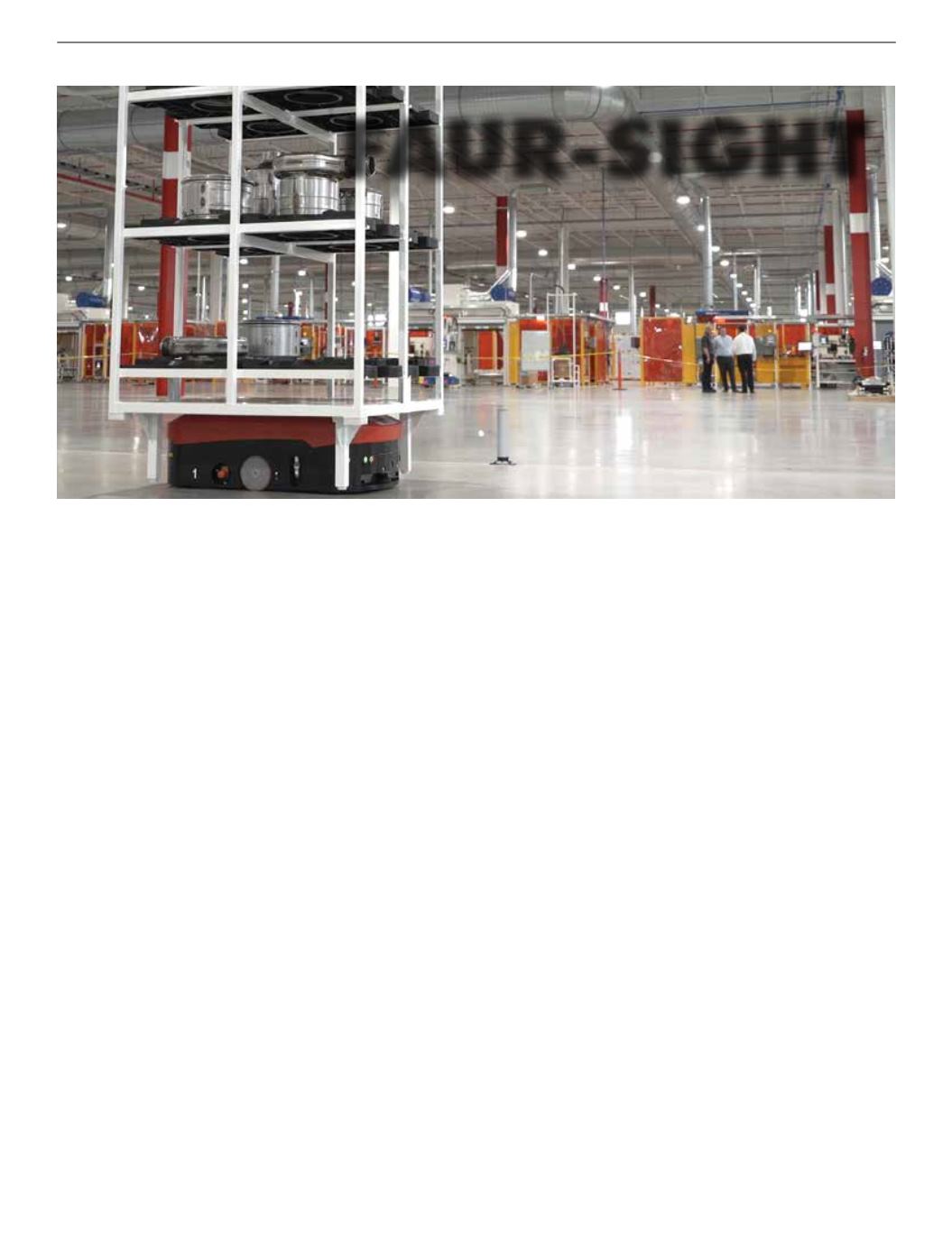
38
BizVoice/Indiana Chamber – September/October 2017
Walk along the floor of Faurecia’s
new Columbus South plant and
one may feel as if he’s in a
Transformers
film. Sturdy machines
lift emissions components with
ease like a professional wrestler
preparing for a body slam. That
slam, however, is replaced by
delicate, precise placement in
advance of a welding operation.
Robots are also seen working alongside
people and autonomously rolling through,
focused on a mission of transporting racks of
parts throughout the facility.
Faurecia is North America’s eighth largest
automotive supplier. Its global headquarters is
in France and the company has operations in 35
countries with a network of 300 production
sites and research and development centers.
Although its Columbus South operation
focuses on emissions control, Faurecia also
specializes in automotive interiors and
seating. Customers include Ford, General
Motors, BMW, Hyundai, Nissan and
Volkswagen, and it has a partnership with
Cummins Emissions Solutions.
‘My co-worker is a robot’
V-Cell operator Misty Lang points out
her workstation during a tour. She relishes
the job, which she’s held for nine months, and
remarks how the fast pace of the work gives
her energy. While the work is expeditious,
she celebrates that the new technology has
alleviated the need for heavy lifting – a
trademark in some manufacturing jobs.
A Seymour resident, Lang had worked
in the manufacturing and education fields and
wanted to do something different. She admits
that working with robotic teammates was an
adjustment.
“The robots were overwhelming at first,”
she says. “I was thinking, ‘I’m going to be in
charge of that robot? They cost millions of
dollars.’ ”
Yet Lang has come a long way on the job
in just nine months, now serving as a tour
guide to this reporter after having recently
made a presentation to suppliers.
She points out the many streamlined
operations at Faurecia – a company so innovative
it filed for over 500 patents in 2016 alone.
Lang lauds the geographic diversity of her
co-workers, many of whom hail from other
states and countries at the international company.
Collaborative robots, known as “cobots,”
are found throughout the 400,000-square-
foot facility.
“(Cobots) do some of the more highly
repetitive, lower-skilled work, like pick and
place,” explains David DeGraaf, president of
Faurecia Clean Mobility North America.
“Instead of having someone do that all day
long and risk repetition injuries, a cobot can
do that. They have sensors so if an employee
bumps it, it will stop. It’s conducive to
working alongside somebody.”
“Our stacking stations are the biggest
example of co-existing robots and the human
worker,” elaborates Mike Galarno, plant manager.
“The employee is standing in the cell, putting
the gasket on the V-band flare and Marmon
Joint located between the two modules.
There’s no wall between the worker and the
robot except for a light curtain. It’s a little
unique in that you don’t have the full caging
around the system, so they have to co-exist in
the same environment.”
Screenshots
The modern societal inclination to stare
at screens can be irritating for anyone who’s
been bumped into by an enthralled pedestrian
or for a teacher attempting to capture a
student’s attention. Before the $64 million
Columbus South location opened in 2016 and
launched its “Digital Enterprise 4.0”
approach, managers were spending a great
deal of time posting data to visual boards.
That process is now completely digitized with
touchscreen monitors.
Information can also be sent immediately
via text or email to staff, customers or
suppliers. Screens can be written on or
marked up directly and data from the past can
be quickly accessed and analyzed.
“As soon as something happens on the
line, I can have a notification on my phone,”
DeGraaf illustrates. “We can track the issue,
who’s working on it and (the estimated time)
to get back online. Our maintenance team
can manage different parameters of how that
equipment’s running – cycle time, energy
usage, any type of anomaly that’s happening.
Robots, Technology
Dominate Plant Floor
FAUR-SIGHT
By Matt Ottinger
Technology and Innovation: Yearlong Series